Last quarter we had some difficulties integrating our system on Unity. Toward the end, with some help from a fellow student in computer science, we were able to figure out a lot of the kinks within our code. We are still dealing with optimizing the code and are in the process of 3D printing our controller. What we decided on doing for the controller is make a base that can then have attachments on the outside. This way, the controller can be transformed to an animal or person, like a doll. We went through our first iteration of the 3D model and have had it printed. We look to modify it and have a second version printed by next week once we figure out some of the issues with the first design. We are housing the components in a drawer compartment. We mainly used our first print to test the fit since we went and individually toleranced each side/fit of the 3D model.
For the second iteration of our electrical components we are working on developing a PCB board schematic. Although we have that in our deliverable, when consulting a recently graduated electrical engineer about it, he suggested using a perforated board. This would be more cost effective and easier to manipulate, especially since a few of us have soldering experience. The one downfall would be it would not look as professional. We have thrown around the idea of doing both and seeing which one works best.
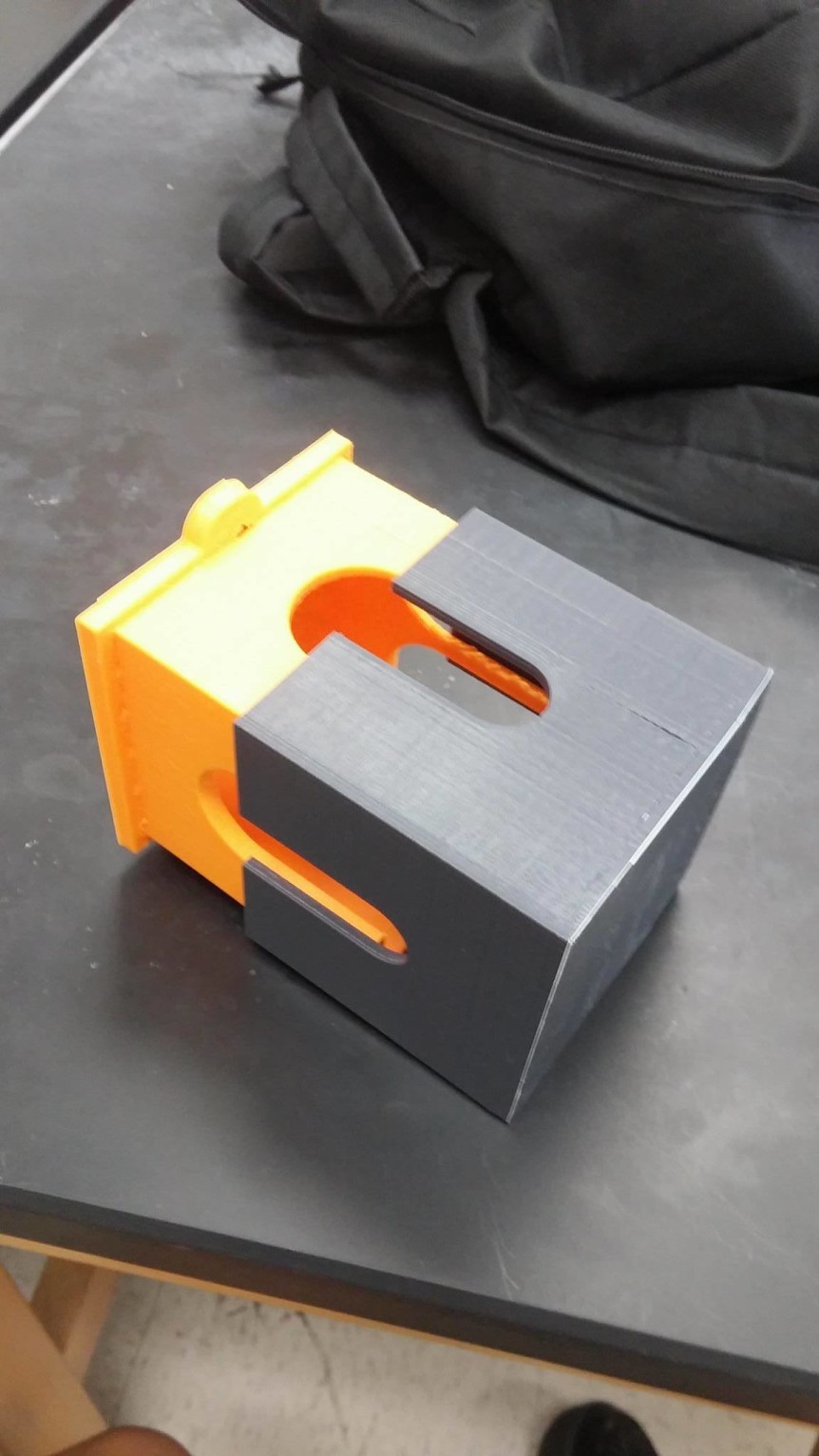